3Dモデルで学ぶ射出成形機の各部位の名称と役割
- SANKO GOSEI
- 2月3日
- 読了時間: 4分
射出成形は、プラスチック製品の大量生産に欠かせない製造方法です。その中心となるのが「射出成形機」です。射出成形機にはさまざまな部位があり、それぞれが重要な役割を果たしています。本記事では、3Dモデルを活用しながら、射出成形機の各部位の名称と役割を詳しく解説します。
1. 射出成形機の基本構造
射出成形機は、大きく分けて以下の3つの主要部分から構成されます。

射出装置(Injection Unit) - 樹脂を溶かして金型に射出する部分
型締装置(Clamping Unit) - 金型を開閉し、成形時の圧力に耐える部分
制御装置(Control Unit) - 機械全体を管理・制御する部分
それでは、それぞれの部位を詳しく見ていきましょう。
2. 射出装置(Injection Unit)
射出装置は、プラスチック材料を溶融し、金型内に送り込む役割を担います。主な構成部位は以下の通りです。
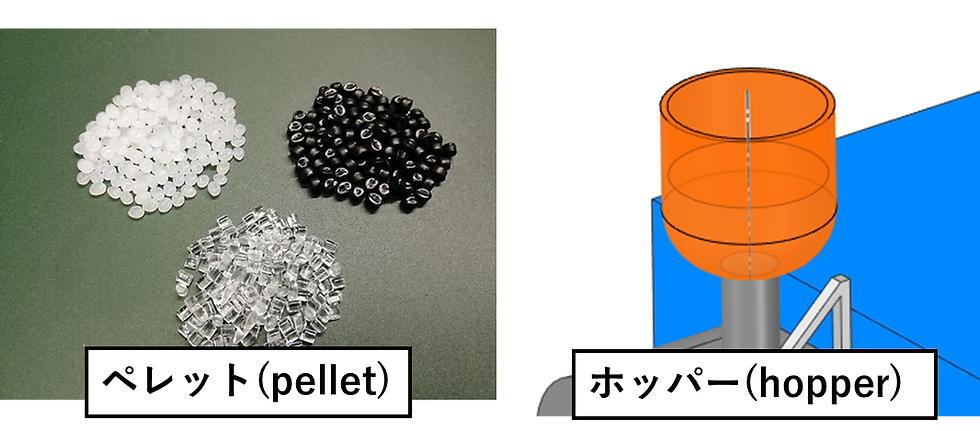
(1) ホッパー(Hopper)
ホッパーは、成形材料(ペレット状の樹脂)を投入する部分です。通常、乾燥機と組み合わせて使用され、吸湿しやすい樹脂(例:ナイロン)には、乾燥処理を施してから供給します。

(2) シリンダー(Cylinder)
シリンダー(バレルとも呼ばれる)は、ホッパーから供給された樹脂を加熱し、溶融する部分です。内部にはスクリューが配置されており、樹脂を前方に送るとともに、均一に溶かします。
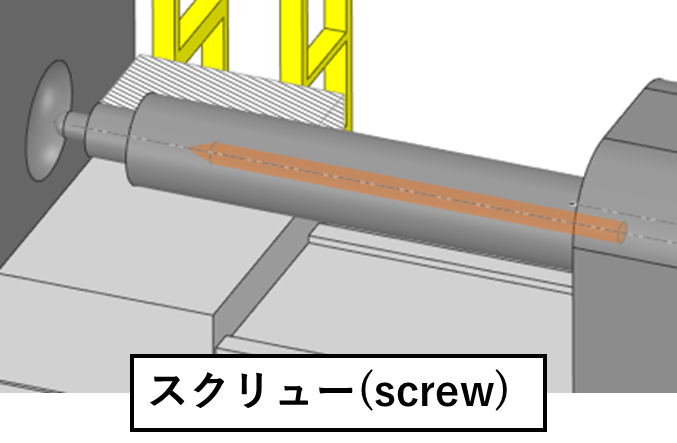
(3) スクリュー(Screw)
スクリューは、樹脂を効率よく溶融し、混練する重要な部品です。スクリューの形状やピッチによって、成形品の品質が大きく左右されます。
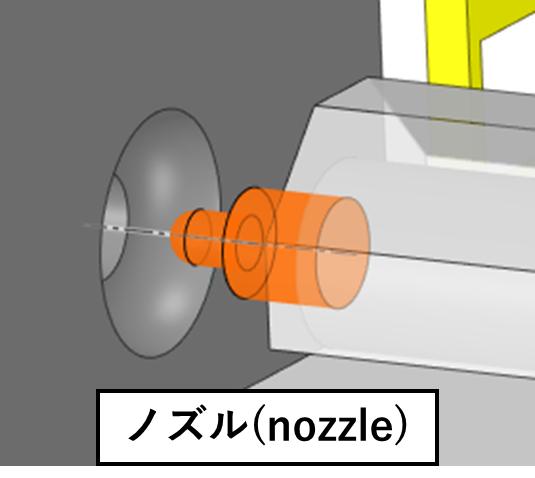
(4) ノズル(Nozzle)
ノズルは、シリンダー内で溶融された樹脂を金型内へ送り込む部分です。ノズルヒーターによって温度を調整し、樹脂の流動性を確保します。
3. 型締装置(Clamping Unit)
型締装置は、金型を開閉し、射出時の高圧に耐えるための機構です。主な構成部位は以下の通りです。
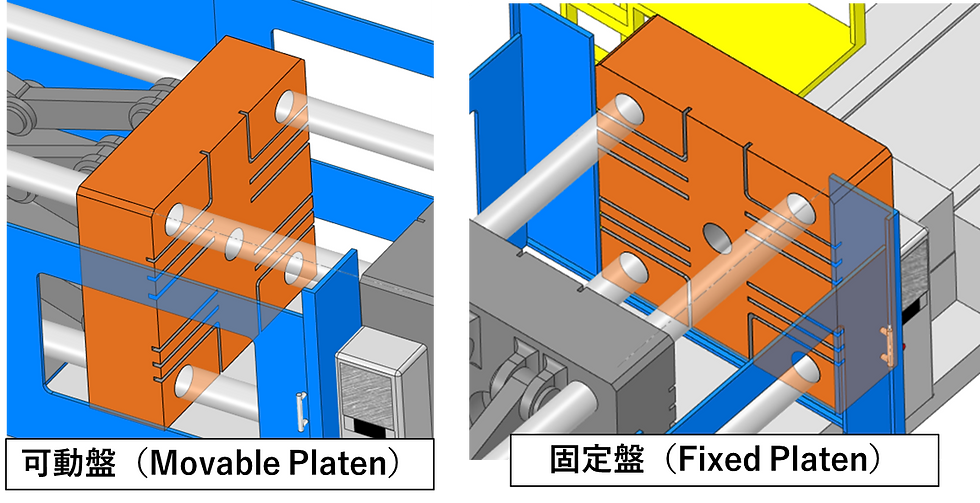
(1) 可動盤(Movable Platen)・固定盤(Fixed Platen)
金型は、可動盤と固定盤の間に設置されます。固定盤は機械のフレームに固定され、可動盤がスライドすることで金型が開閉します。
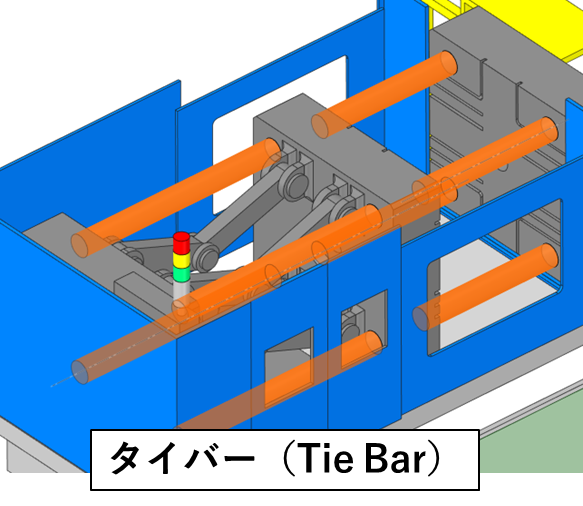
(2) タイバー(Tie Bar)
タイバーは、可動盤と固定盤を支える4本の強固な金属棒です。型締力を均等に分散させ、金型の変形を防ぐ役割を担います。
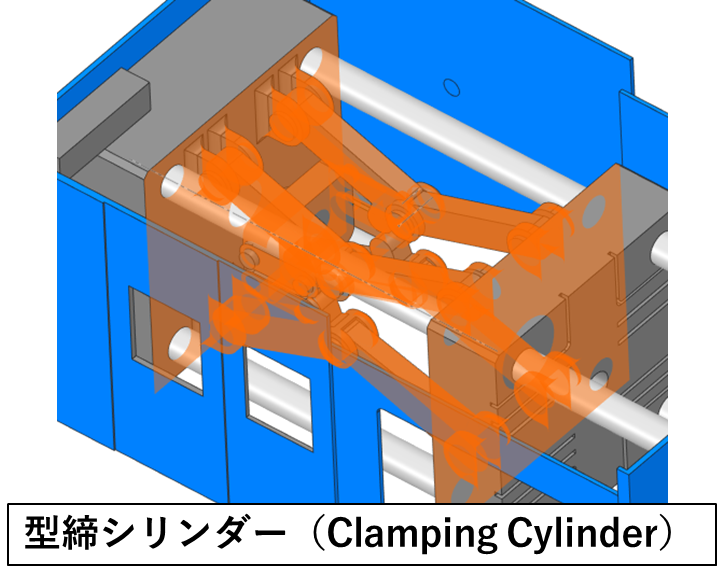
(3) 型締シリンダー(Clamping Cylinder)
型締シリンダーは、油圧または電動式で可動盤を押し込み、金型をしっかりと閉じる役割を果たします。射出時の高圧に耐えられるよう、適切な型締力を設定することが重要です。

(4) エジェクタ(Ejector)
成形品を金型から取り出すための機構です。エジェクタピンが前進し、製品を押し出します。エジェクタの動作が不適切だと、製品が金型に貼り付いたままになることがあります。
エジェクタの多くは可動盤に装着されます。
4. 制御装置(Control Unit)
射出成形機の動作を管理し、適切な条件で成形を行うためのシステムです。

(1) タッチパネル(Touch Panel)
近年の射出成形機には、操作用のタッチパネルが搭載されており、温度、圧力、射出速度などを設定・監視できます。
(2) センサー(Sensors)
温度センサー、圧力センサー、位置センサーなどが搭載されており、リアルタイムでデータを取得し、成形条件の最適化を行います。
(3) サーボモーター(Servo Motor)
電動射出成形機では、サーボモーターを使用してスクリューや型締機構を精密に制御します。エネルギー効率が高く、精度の向上にも貢献します。
5. まとめ
射出成形機は、単なる「プラスチックを流し込む機械」ではなく、各部位が緻密に設計され、連携しながら成形を行う精密機械です。
主要部位のおさらい
✅ 射出装置:ホッパー、シリンダー、スクリュー、ノズル
✅ 型締装置:可動盤・固定盤、タイバー、型締シリンダー、エジェクタ
✅ 制御装置:タッチパネル、センサー、サーボモーター
これらの部品の理解を深めることで、より高品質な成形を実現できます。特に、成形不良やトラブルの原因を特定する際には、各部位の役割を正しく把握しておくことが重要です。
3Dモデルを活用しながら、ぜひ実機で確認し、理解を深めてください!
Comments